The world of industrial packaging is vast and complex, with FIBC (Flexible Intermediate Bulk Containers) stitching standing as a pivotal element. In the past decade, the use of FIBCs has surged due to their versatility, efficiency, and cost-effectiveness in handling bulk materials. In this nuanced domain, the FIBC sewing machine emerges as a cornerstone, meeting the demand for high-quality and robust containers essential for various industries.
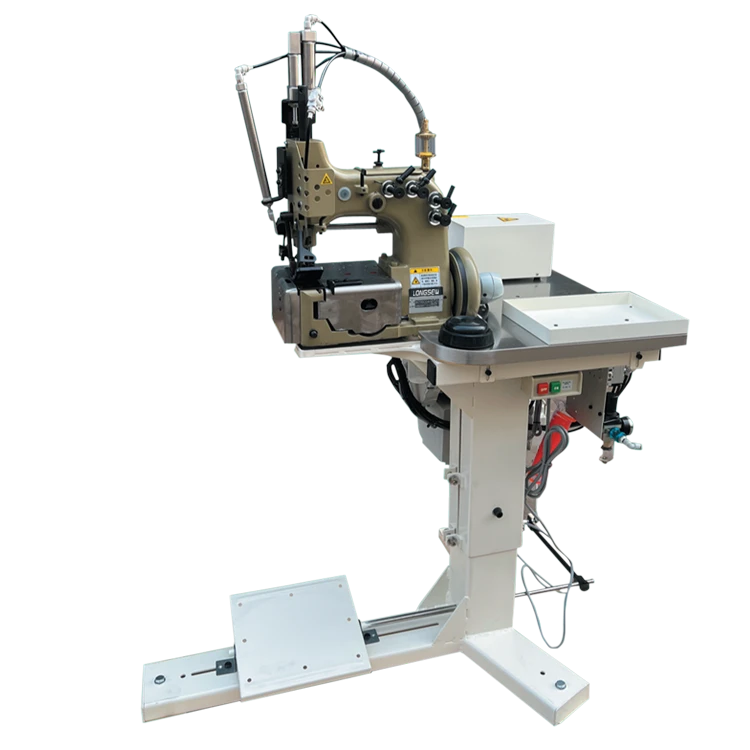
The FIBC sewing machine, in its essence, has revolutionized how businesses approach packaging by introducing precision, speed, and durability in construction. These machines are specifically designed to cater to the heavy-duty requirements necessary for creating FIBCs that carry anywhere between 500 to 2,000 kg of material. What sets these sewing machines apart is their ability to handle heavy fabrics, such as woven polypropylene, which are indispensable for FIBCs.
A real-world experience from a leading textile company highlights the impressive capabilities of modern FIBC sewing machines. By integrating an advanced automated sewing line, the company was able to increase its production capacity by 40%, while simultaneously reducing fabric wastage by 15%. This transformation is credited to the machine's precision and ability to produce consistent stitch strength, ensuring that each FIBC meets stringent safety standards. Enhanced features such as programmable logic controllers (PLCs) allow for sophisticated pattern stitching, vital for reinforcing areas that bear the most strain.
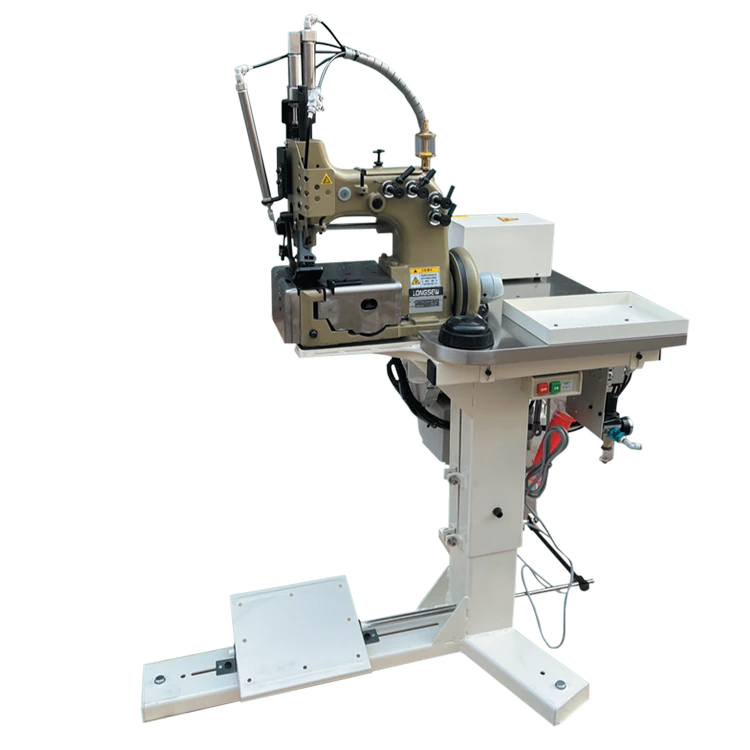
When examining the expertise involved in operating an FIBC sewing machine, it's notable that these machines require skilled technicians, due to the intricate nature of their operation. Training focuses on understanding the machine's intricate parts, such as the stitching head and conveyor belts, and their harmonized performance. Mastery of these aspects ensures minimal machine downtime and optimal throughput, underscoring the importance of expertise in leveraging technological advancements.
fibc sewing machine
Moreover, the breadth of specializations in FIBC sewing machine development is often overseen by leading textile machinery manufacturers. These firms invest substantial resources in research and development to ensure their machines align with the latest industry standards and consumer needs. Some incorporate AI-driven diagnostic tools to preemptively address maintenance issues, a testament to the authority these manufacturers hold in driving innovation within the industrial sewing sector.
The trustworthiness of FIBC sewing machines is critical, as their outputs are expected to perform under extreme conditions. For instance, an agriculture company relies on these machines to produce bags that store grains, which endure various environmental factors. The bags need to be reliable, as any failure could result in significant financial losses. By choosing machines from reputable manufacturers known for rigorous testing and quality assurance processes, companies can trust that their packaging solutions will hold up under pressure.
Trust is not just built on machine performance, but also on post-purchase support.
Establishing robust networks for after-sales service maximizes the operational lifespan of FIBC sewing machines. Leading manufacturers offer extensive service contracts, regular machine audits, and genuine replacement parts to uphold machine reliability. This layered approach not only secures consumer trust but also ensures long-term collaboration.
In summation, the advancement and specialization of FIBC sewing machines underscore their indispensable role in modern industrial packaging. They embody a synergy of experience, expertise, authority, and trustworthiness—each aspect diligently refined to enhance the functionality, reliability, and efficiency of large-scale packaging solutions. These machines are not only a testament to innovation in the sewing machine industry but are also pivotal in shaping how industrial packaging solutions evolve in response to growing global demands.